Recycle paper, not ideas
At Kärcher, we think globally – the role of the sustainability manager was created to ensure that the Kärcher sites across the world are equally committed to advocating sustainability. Three managers explain the significance of their work and which unique regional challenges they are coping with.
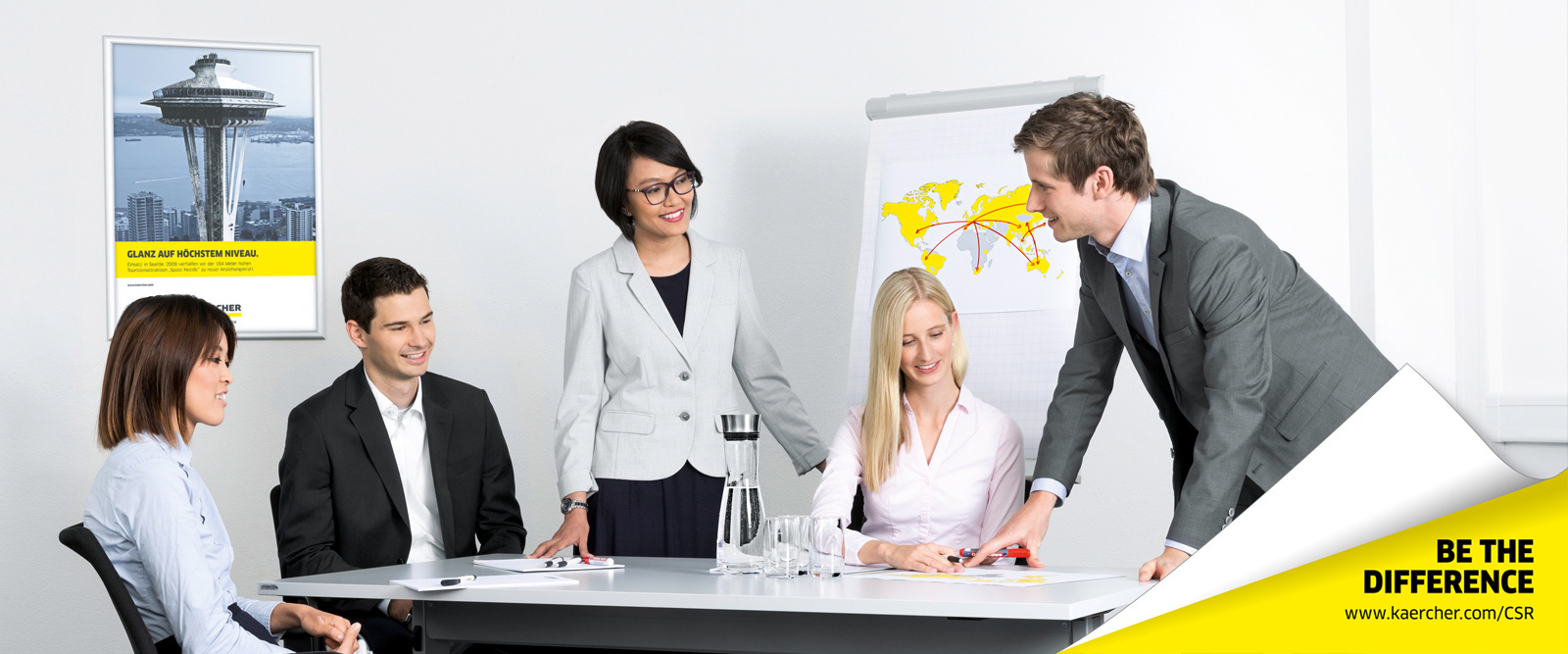
Mr Fang, which particular challenges are you facing in relation to sustainability in your country?
The Chinese economy has recently been growing rapidly. So the environment and finite resources have been greatly affected. In the last few years, however, China as a whole has been increasingly recognising the significance of sustainability and environmental protection. The number of green initiatives – by both companies and the public – has greatly increased. In my opinion, Kärcher China is already well on the way in terms of these issues.
Do you have examples of measures that you are taking to increase sustainability at Kärcher China?
In China, service providers and suppliers often still don't have a direct grip on sustainability and the environment. That is why we pay particular attention to training both new and long-standing suppliers in the issues of sustainability and the environment. If the conditions are right – i.e. the distance allows for it – we hold workshops on site and offer interested colleagues from other departments in-house training in our plant. In addition, we always check material management based on the global Kärcher purchasing guidelines before signing a contract. We also regularly check the work of the suppliers as the process goes on.
Where is the current focus at Kärcher China?
For us, prevention is especially important. We already pay attention to sustainability and environmental protection in production and the supply chains. In terms of the relevant standards, we follow the central specifications of the Kärcher Group and are consequently often ahead of other companies in China. So we have already advanced a long way when it comes to digitalisation in our offices and have, for instance, greatly reduced paper consumption. In addition, we train our employees in issues such as resource conservation. I personally am very proud of my employees, who are enormously motivated to promote these issues.
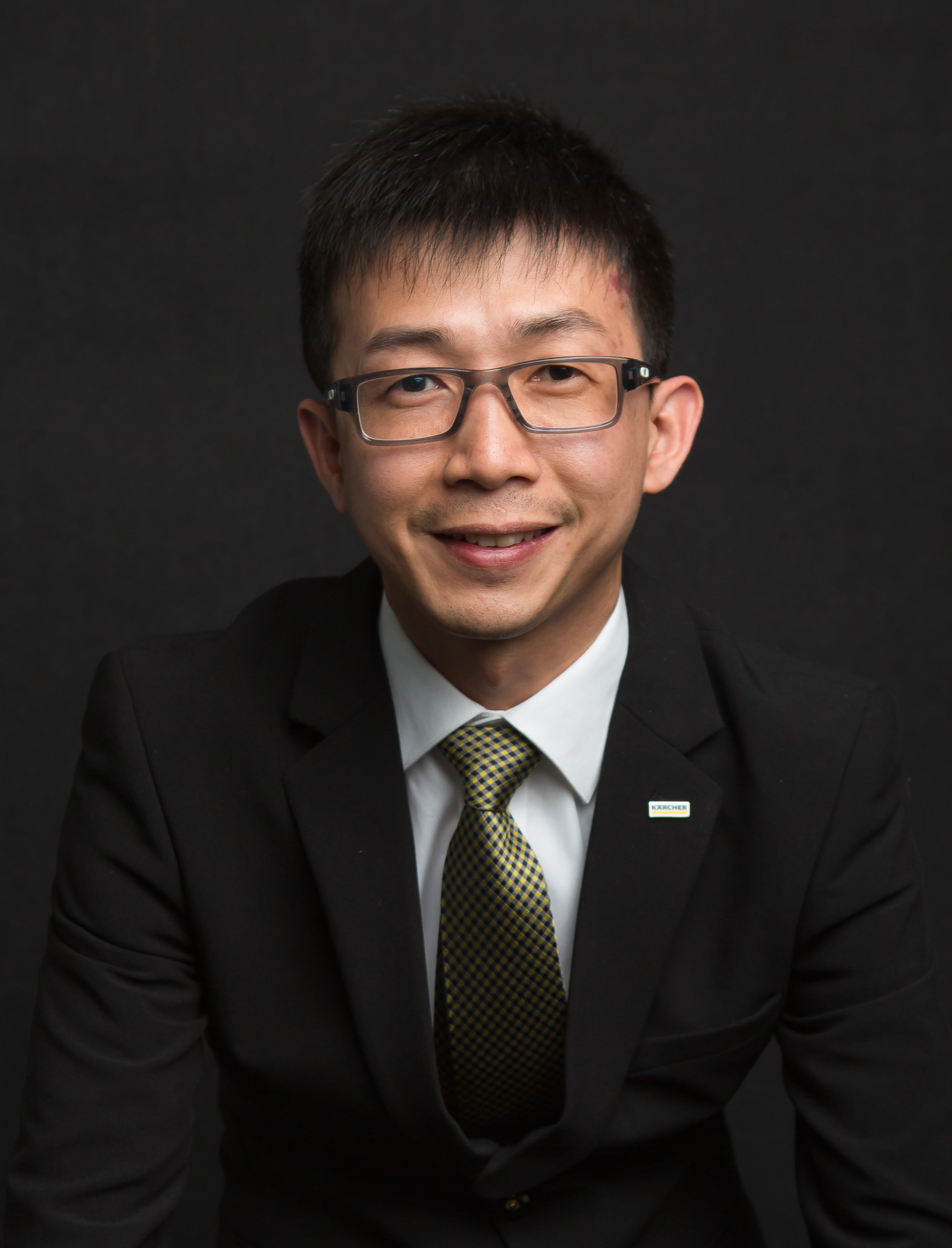
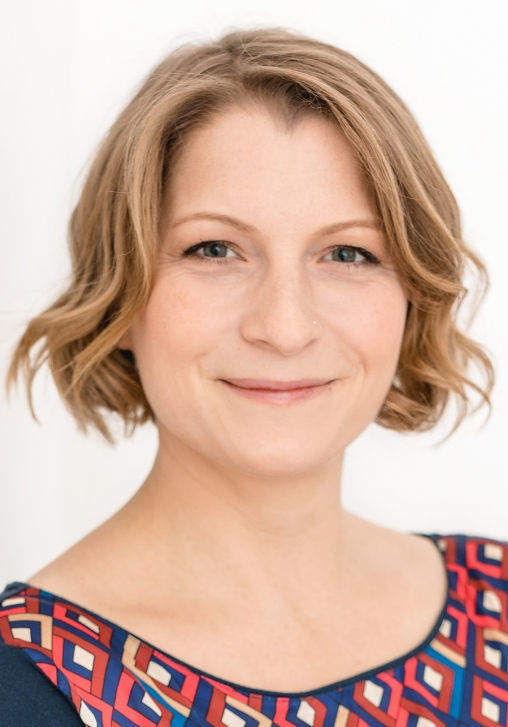
Ms Peintinger, what significance has sustainability in Austria?
Compared with other countries, Austria is certainly already well-positioned. In the areas of rubbish separation, recycling and energy efficiency, it has already done a lot in the last few years. In terms of renewable energies, Austria has a great locational advantage when it comes to water force. The people here have a pronounced awareness of their environment, and I also see that with my colleagues. The issue of sustainability is of great personal importance to the employees. They want Kärcher to become even more sustainable and want to be an active part of this. And that is also very important, as there is naturally still much to do, for instance when it comes to reducing CO2.
As a sustainability manager, how do you serve the interests of employees?
I personally see myself as having an interdisciplinary function across all areas and as a point of contact for all issues relating to sustainability. As a first step, therefore, I went through discussions with managers and employees and got ideas and suggestions from there. The feedback was very positive and as a result of this, an issue-based focus group of interested colleagues has formed, and we are currently developing a catalogue of measures. With a regular newsletter, I inform colleagues of current developments relating to the issue of sustainability, inside and outside the company.
Which issues are particularly topical in your view?
One of my first subjects was disposing of and recycling lithium-ion batteries. As we have more and more cordless devices in our range, that is a highly topical issue. In close coordination with our dangerous goods and waste manager, we found and commissioned a company that provides collection points in our Kärcher centres and handles correct disposal from preparation up to recycling. This allows at least 75 per cent of raw materials to be extracted from the batteries for recycling.
Ms Leal, how does sustainability management look in Brazil, and at Kärcher in particular?
In Brazil, people are not yet so aware of environmental issues and the subject of sustainability. It can, therefore, be difficult to create and share visions that attract attention – both with colleagues and with customers and third parties. That can be seen already with issues like rubbish separation and recycling, which are simply not relevant in Brazil for the most part.
This is why environmental, sustainability and quality issues are directly integrated into the training of new employees at Kärcher. We explain initiatives like the reduction of paper consumption at the workplace, the use of glass instead of plastic for water and so on.
Due to the fact that we follow the specifications of the German parent company, we already have a higher standard than is stipulated in Brazil. Both in production and in our offices, we have, for instance, the possibility of sorting different types of rubbish such as paper, glass, plastics, organic materials, etc. Completely doing without paper is currently a challenge for production, as it is still in the process of digitalisation. But here too, we are forerunners compared with the rest of the country.
In your view, has awareness of this issue changed?
Awareness of sustainability has grown in the last two years, and certainly not only in public. More and more companies see it as a separate pillar in their strategies. At Kärcher Brazil, we are always in communication with other large companies in the country about issues of sustainability and the environment, and also work on joint ideas.
What are you planning to do to forward sustainability?
I personally find it important to also make family, friends and colleagues aware of this issue. Rubbish separation and recycling are especially difficult to teach in Brazil. Many people in Brazil think, for example, that we take away work from the rubbish separators who work on the street if we do not simply dispose of our rubbish on the street, but separate it ourselves at home or in the office. That inspired us at Kärcher to plan an environmental week for our employees. The idea behind this is to carry out a whole week of training, meetings and events relating to the issue of sustainability. Building on this, we can then develop training for our service providers and suppliers.
What acted as great inspiration for me was the Kärcher sustainability breakfast, at which I had the opportunity to come together with people from different departments and countries. I found the exchange of different positions and points of view between colleagues very helpful and inspiring.