Silo cleaning in agriculture
Flat or mobile silos, high silos, silo bags made of Trevira – there are various ways to store fermented and dried feed, other fodder components and slurry. If there is a lack of hygiene on the farm, contamination will cause performance losses and health problems for the animals. Thorough silo cleaning is necessary after each storage period to prevent this.
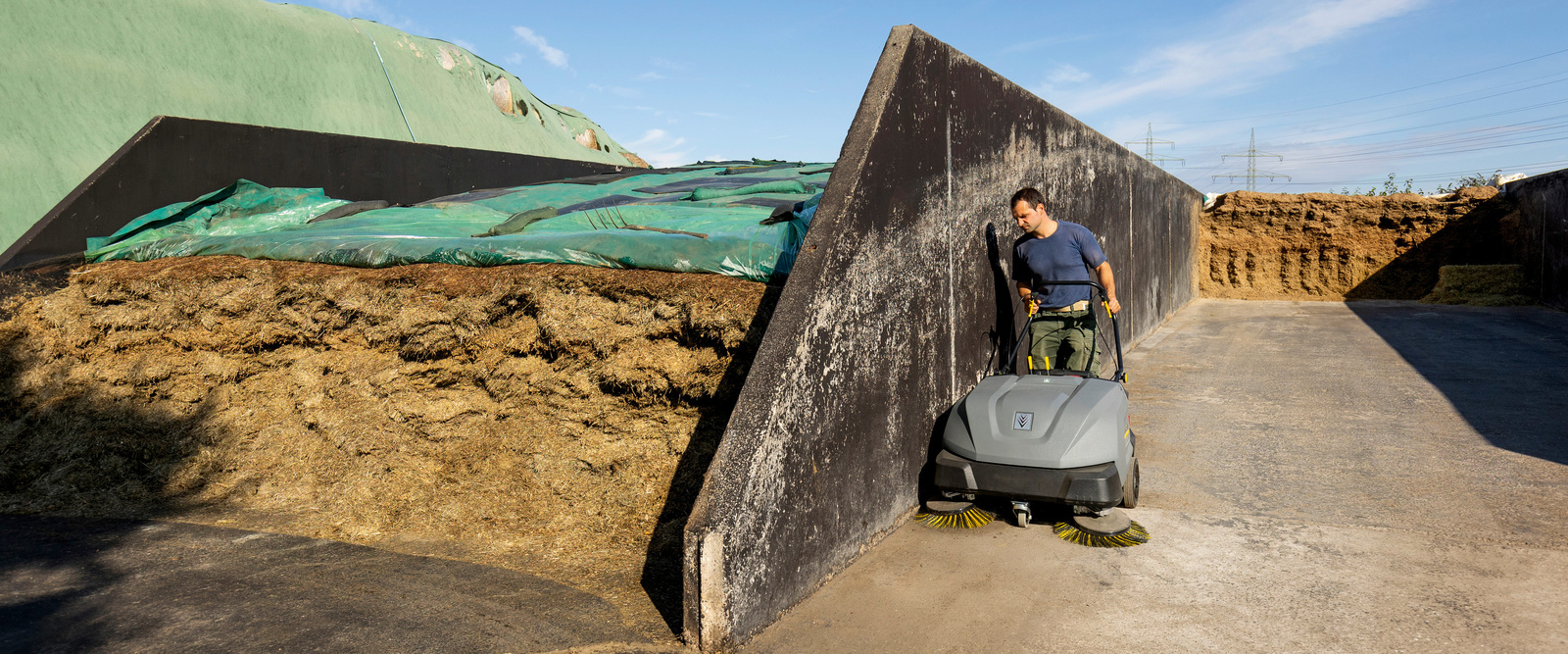
Why clean silos? Legal requirements and economic necessity
The immune system and the health of animals are supported by a stable intestinal flora. For this, they need cleanly fermented feed and the lactic acid bacteria that are very important for the intestinal flora. According to the respective applicable feed hygiene regulations, farmers who produce, process and store feed must comply with clear specifications regarding cleanliness and hygiene. Inspection and cleaning of feed silos in a fixed cycle is therefore just as obligatory as the documentation of the measures. But the legal framework is not the only reason for farmers to regularly check cleanliness and hygiene in the feed cycle and to carry out the necessary cleaning work – it is also a matter of economic success.
What a lack of hygiene does to the feed cycle
If, for example, moisture penetrates a silo bag with dry feed, the feed absorbs the moisture and fungus develops. If this is not noticed, spores can be detected in the feed, which can lead to health problems in the animals. If deposits of feed residues and mould get into the feed in outdoor silos, the animals' performance will be significantly reduced. Sows may fail to lactate, pregnancy and farrowing rates decrease, and the remating rate increases. The contaminated feed can lead to diarrhoea, the lower feed intake results in reduced gains during fattening, which prolongs the length of time the animals are kept. The economic losses can be immense if the hygiene risk is not localised and eliminated. Consistent control and regular silo cleaning ensure that such problems do not occur in the first place and that animal health is maintained.
Cleaning bunker and flat silos: lots of pressure, lots of water
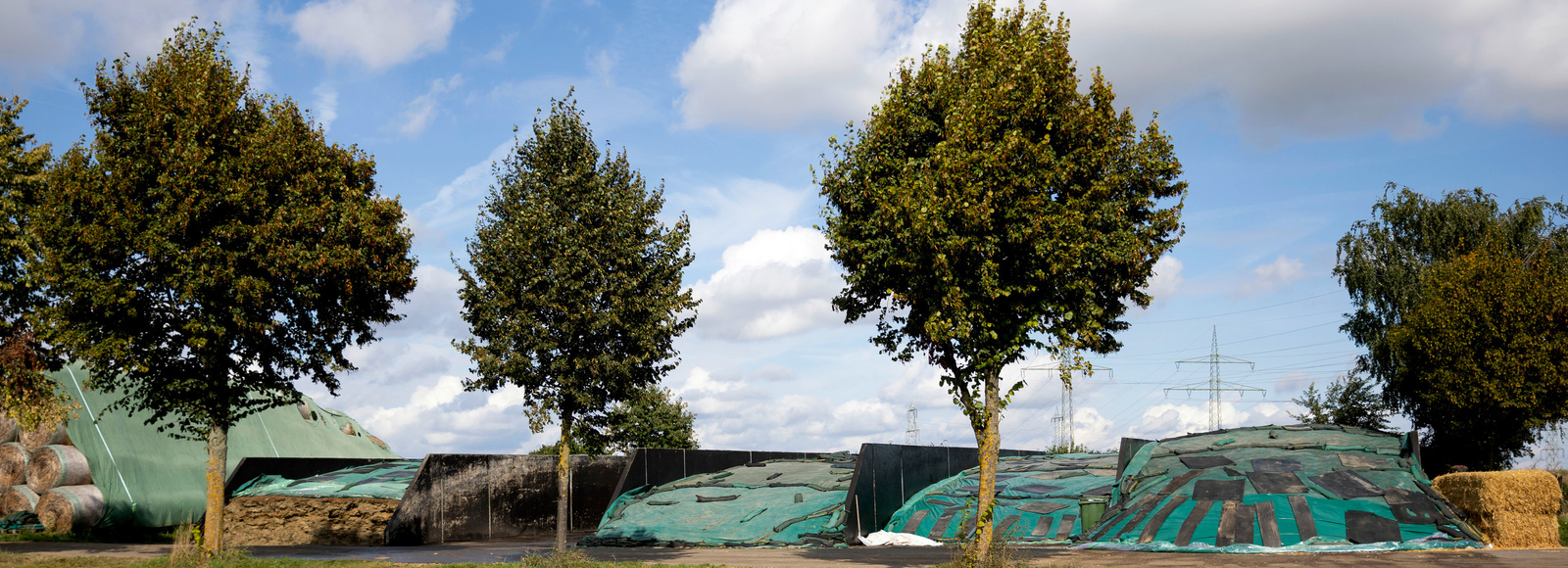
Bunker or flat silos are made of concrete and are either lined with tar or coated with a bitumen silo varnish. This protects the floor and walls against aggressive seepage and stress caused by machinery. However, wind, weather and other external influences make the surfaces more porous over time, so that feed residues and dirt settle more easily – an ideal living environment for germs and mould. Every time the silo is emptied, it must be thoroughly cleaned so that newly stored fodder is not spoiled.
A high-pressure cleaner that delivers a high pressure of up to 250 bar as well as high water volumes of up to 2,500 litres and has a high flushing capacity is very well suited for this work. This is the only way to loosen and remove stubborn dirt with waterpower. A dirt cutter, i.e. a rotating nozzle that produces a moving round jet, is a useful accessory for increasing performance. If the silo has high walls, telescopic lances help to reach all surfaces. Clean the walls then the floors at a working distance of about 40 centimetres.

PPE and more: protective gear for silo cleaning
Personal protective equipment (PPE) is required to protect against flying dirt particles or detached pieces of concrete. This generally includes a protective suit, gloves, boots, safety goggles and hearing protection. To protect yourself from potentially swirling germs, use full-body protective suits, air filter masks and high closed boots when cleaning silos. The dirty water must be disposed of properly in accordance with the regionally specified public discharge regulations.
Tip 1 – ergonomics:
Ergonomics is also an important issue in agriculture, especially as silo cleaning involves a high level of physical strain. Ergonomic accessories such as the EASY!Force high-pressure gun, for example, use the recoil force of the high-pressure jet and reduce the required holding force to a minimum.
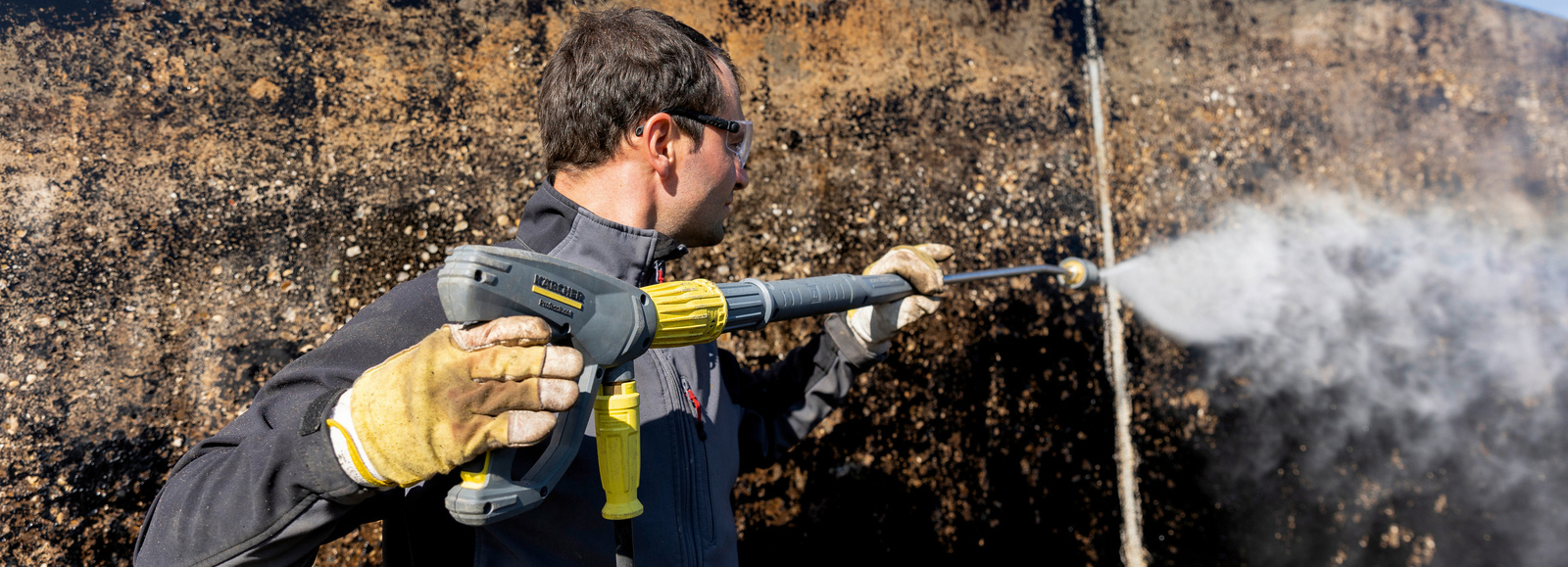
Tip 2 – cleaning the PE film:
A flat-jet nozzle is very suitable for cleaning the PE film used to cover the silos. Reduce pressure and water quantity to avoid damaging the film.
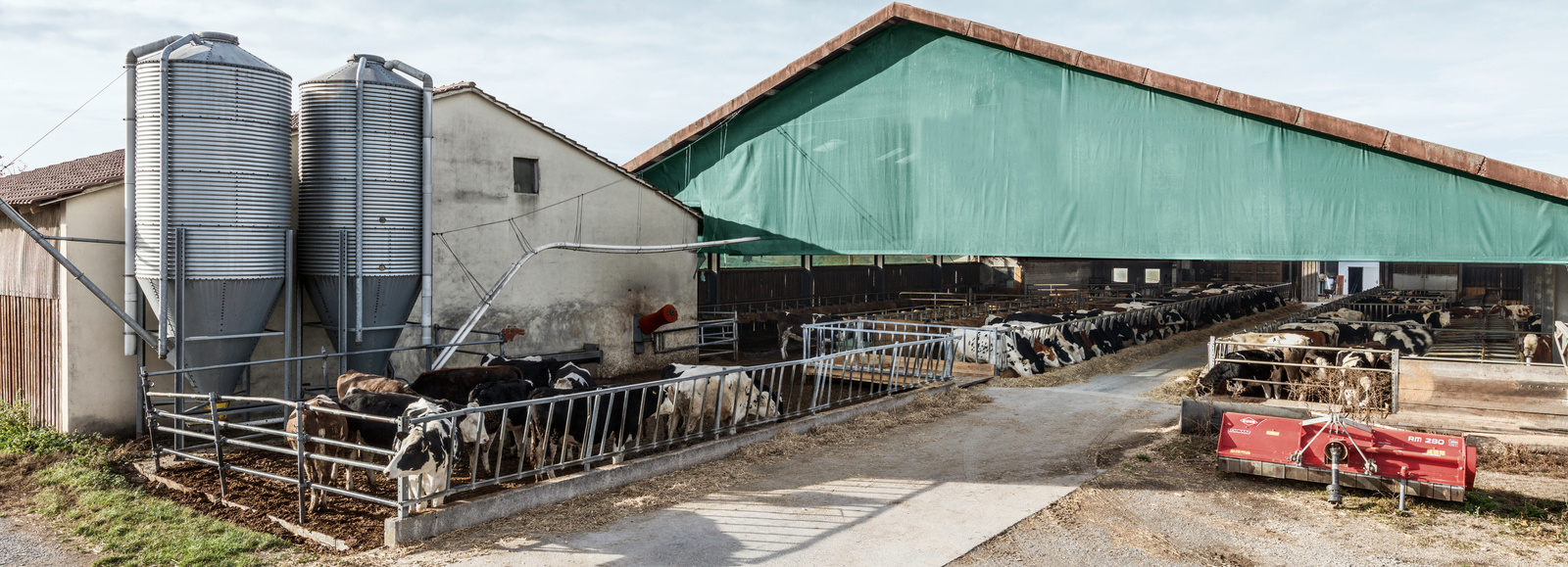
Cleaning tower silos from the outside and inside
Outdoor silos or high silos, which are built into a three- or four-leg system, are widely used. It is crucial for the quality of the stored goods that the silos are tight and that no water penetrates via seams, service flaps or the fodder intake. This is because both moisture coming from outside and the condensation that occurs at high temperatures pose the risk of deposits forming in the silo. It is therefore important to clean the silo thoroughly after each emptying. Otherwise, mould and germs will form in the deposits over time, which can get into the feed and damage animal health. Exterior cleaning includes the walls as well as the silo hopper for feed removal. It is recommended to work with a hot water high-pressure cleaner to effectively remove feed residues, mould and other impurities.
Dry silo cleaning via the inspection hatch
If internal cleaning is required, you can do this via an inspection hatch that is either recessed in the silo lid or retrofitted as a service hatch. If necessary, remove dry deposits via the hatch from the outside with a telescopic lance and a wet and dry vacuum cleaner. Vacuum off loosened dirt via the extraction hatch. Depending on the types of dust to be extracted, class M or H filters may be necessary. Another criterion is explosion protection according to current ATEX specifications, the European directive on explosion protection (Atmosphères Explosibles). This ensures that vacuum cleaners do not pose a danger when handling flammable substances – the required protective measures vary depending on the ATEX zone (20, 21 or 22).
Dust classes and their meaning
- Class L vacuum cleaners are suitable for extracting softwood, lime and plaster dusts or rubbish. L-class dusts pose a moderate risk. No special precautions are prescribed for their disposal.
- Models with class M filters are suitable for extracting dust generated by the following materials: hardwoods, panel materials, paint dust particles, ceramics, concrete and brick.
- Class H vacuum cleaners are suitable for picking up large quantities of safe as well as hazardous/strongly carcinogenic substances such as asbestos dust, lead, coal, nickel, cobalt, copper, cadmium and mould.
Wet silo cleaning
The silo can also be cleaned wet on the inside via the inspection hatch to remove adhering dirt using a high-pressure cleaner and internal cleaning heads driven by the jet of water. The internal cleaning heads rotate due to the water flowing through them and reach every area in the silo. Water flow rate, pressure and speed can be adjusted depending on the level of soiling: For large or particularly dirty containers, a slow rotation speed and a fine spray pattern are better; for smaller or less dirty containers, faster rotation and a coarse spray pattern are better.
In most cases, thorough silo cleaning requires you to enter the container with PPE including breathing apparatus. This is usually done by experts from specialised companies who have climbing training and the necessary equipment. Cleaning is followed by disinfection.

Dry cleaning silage bags made of Trevira
Cleaning indoor silos is relatively easy compared to flat and high silos. The silo bags made of Trevira, a stable and air-permeable fabric, hang in a four-legged iron frame. The fine fabric outer skin lets the air out of the bag when the feed is blown in, but the feed dust remains in the Trevira silo. Once the silo is empty, shake the bag out and tap it to carry any remaining feed down. As the cleaning flaps are usually so small that you can hardly reach them by hand, a powerful wet and dry vacuum cleaner is a good support in the feed silo to completely remove the old feed remains and dirt during cleaning.
What to do if a Trevira silo has become damp
It is important to house trevira silos in dry rooms. If they are housed in enclosures or under plastic covers, condensation water causes problems. This is because the food quickly absorbs the moisture, so that fungus can develop that is harmful to the animals. If a trevira bag has become damp or wet on the inside, shaking it out and vacuuming it is no longer sufficient. In this case, specialist companies should carry out professional silo cleaning, as working with a high-pressure cleaner and air drying does not produce the desired result. In addition, there is always the danger that residual moisture remains in the bag.
A look into feed production: cleaning stationary silos
A hygiene concept including documentation for feed suppliers is vital in ensuring that there are no weak points in your feed cycle. This means comprehensively cleaning both the large underground tanks and silos for feed storage and the containers that are transported by truck or rail.
For the large, stationary tanks or silos, there are automated cleaning processes integrated into the workflows. A stationary high-pressure supply with an efficient high-pressure pump and a hot water steam generator forms the core of the cleaning system. In addition, there are various accessories such as a self-rotating cleaning head and a plant control system tailored to the needs. If required, use acidic or alkaline cleaning agents to increase cleaning performance.
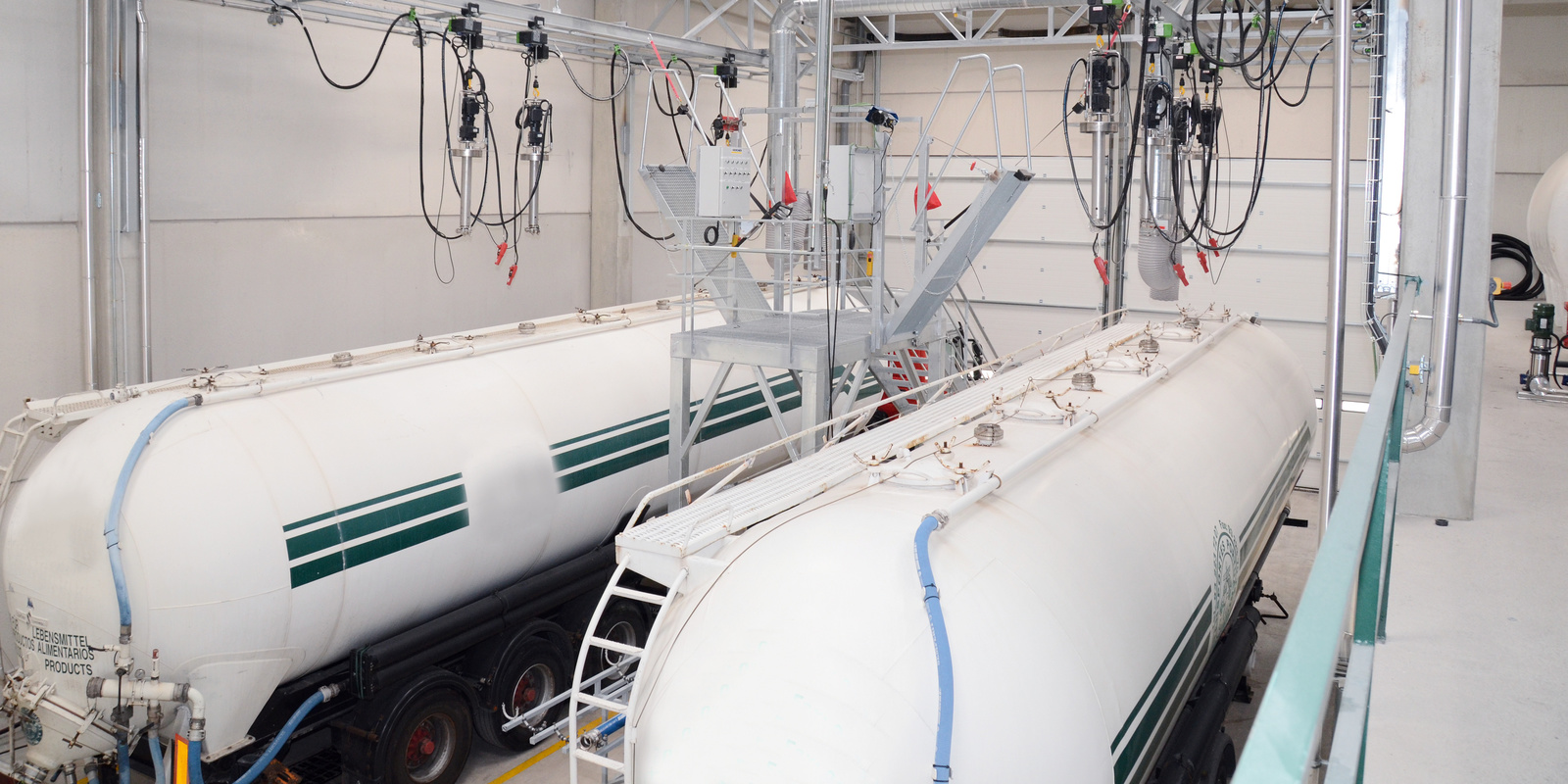
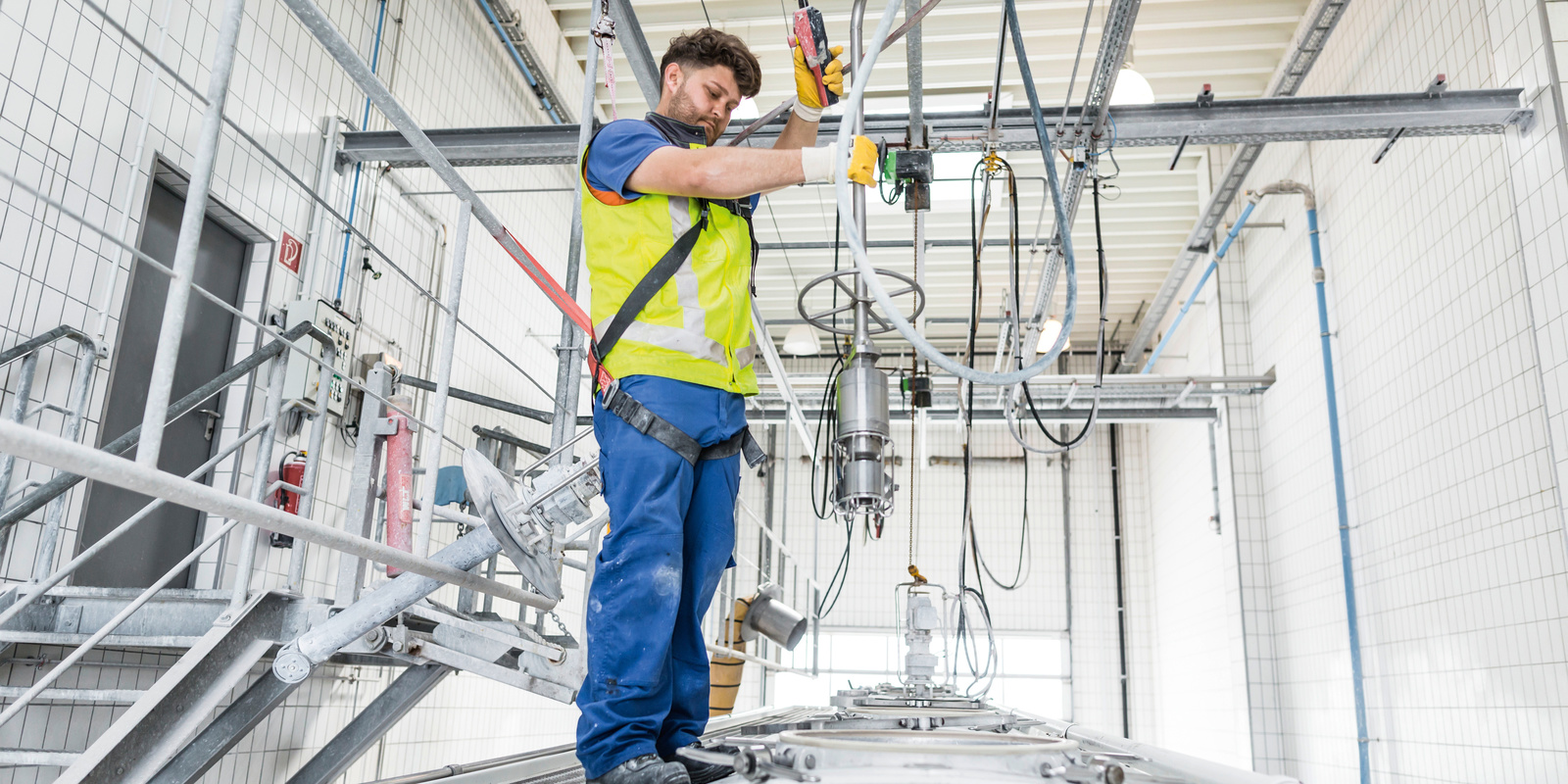
Cleaning mobile containers
Since mid-2015, the EFTCO standard SQAS (Safety and Quality Assessment System) has regulated the cleaning of mobile tanks, containers and silos. The background to this is the increasing safety and quality requirements, which necessitate proof of a continuous cleaning chain from production through storage to transport. For the best possible tank and silo cleaning, the right interaction of mechanics, temperature, cleaning agent and time is decisive. Equipped with a heating system, high-pressure pumps for internal and a high-pressure pump for external cleaning, spray heads, a high-pressure heat exchanger as well as a drying unit, a tank cleaning station ensures fast, efficient and standard-compliant cleaning of mobile containers.
SIDE NOTE: Cleaning out slurry pits from the inside
Slurry silos or slurry pits are usually embedded in the ground, as a prefabricated concrete component or concreted in on site. After complete emptying, it is essential to clean the slurry tank. Wear a respirator and safety belts because of the danger of residual vapours.
- First, pre-water the silo.
- After that, lower a bucket into the silo via a telescopic handler to shovel coarse dirt into.
- Then it is time to carry out thorough cleaning with the cold water pressure cleaner with high flushing capacity, where a dirty water pump is required to extract waste water. After cleaning the silo, dispose of the waste water properly in accordance with the regionally specified public discharge regulations.